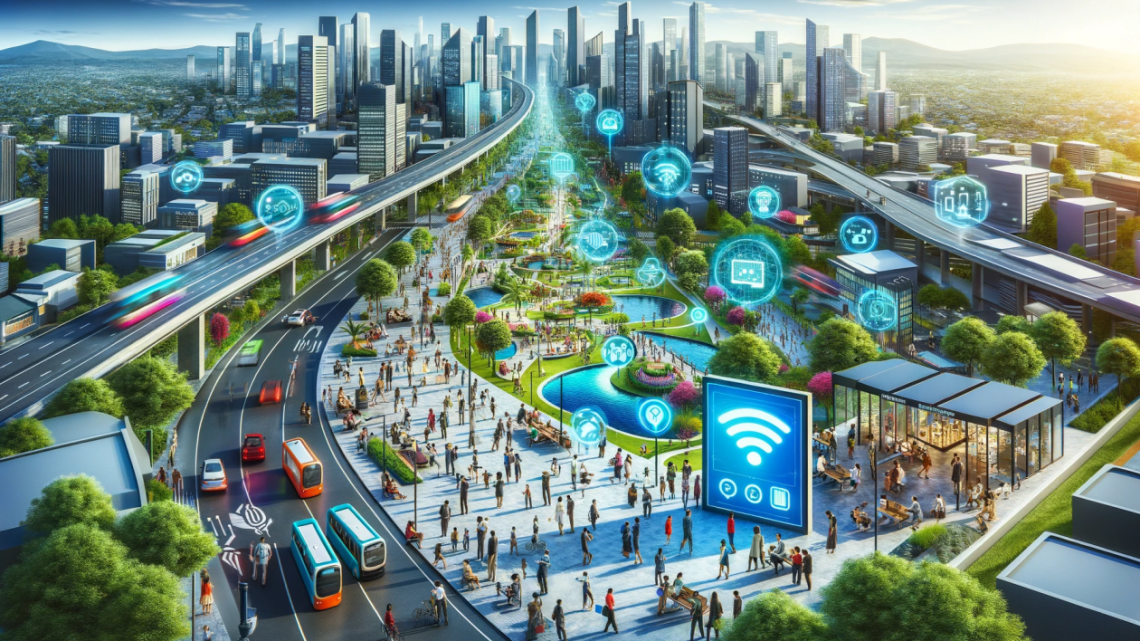
Bridging the Digital Gap in Construction: Challenges and Innovations
May 24, 2024If a worker from the 1920s were to visit a modern construction site, they might be surprised at how familiar it all seems. Despite technological advances in various sectors, the construction industry remains largely unchanged, relying heavily on manual labor. According to Sam O’Gorman, an associate partner at McKinsey, construction in Europe and the US still employs methods akin to those used a century ago.
In 2017, the McKinsey Global Institute suggested that the construction sector could boost productivity by up to 60%, potentially adding $1.6 trillion annually to the global economy. Although there have been strides in improving production processes and incorporating new software and apps, the anticipated level of efficiency gains has not yet been realized. O’Gorman notes that construction lags behind other industries in digital adoption.
Among the innovative technologies poised to transform construction is 3D printing. The University of Maine has developed the world’s largest 3D printer, which constructs houses using a mix of wood fibers and plant-based resin. Their first prototype, BioHome3D, has successfully withstood two Maine winters, prompting plans to build a neighborhood of nine such homes. However, 3D-printed homes remain largely experimental due to their high costs, thick walls, and limited suitability for varied terrains.
Another promising technique is modular construction, where building components are manufactured in factories and then assembled on-site. This method promises superior quality control and fewer on-site errors. Dr. Habib Dagher of the University of Maine advocates for this approach, citing the enhanced finish and precision achieved in a factory setting. Yet, modular construction faces significant hurdles, particularly in the UK, where planning policy delays complicate project timelines, requiring flexibility that the current system lacks.
Bristol-based Automated Architecture (AUAR) offers a potential solution with its micro-factories that use robots to construct timber houses. These micro-factories can be licensed by larger construction firms at a fraction of the cost of traditional modular housing factories. AUAR’s approach promises higher margins for developers, faster build times, and reduced labor costs by up to 60%. The company aims to scale significantly by 2030, targeting the construction of over 30,000 energy-efficient homes annually.
Despite these advancements, the broader construction industry remains resistant to major transformations. However, incremental digital improvements are making headway behind the scenes. Tools for land identification, AI for market predictions, and digital design processes are increasingly common, enhancing various aspects of the construction workflow.
Karoliina Torttila, director of AI at Trimble, highlights the shift from manual record-keeping to digital management of tasks like quantity surveying, health and safety, and carbon emissions. Yet, the fragmented nature of the industry poses a significant challenge to widespread technological adoption. The primary contractor must coordinate numerous sub-contractors, with errors in one area potentially escalating costs in others.
Torttila emphasizes that technology can mitigate these issues. Creating shared 3D models for big projects, for example, can help identify discrepancies early, fostering better communication and planning among teams. This approach not only smooths the construction process but also aids in forecasting, planning, and purchasing decisions.
Conclusively, while the construction industry has been slow to adopt new technologies, incremental digital advancements are beginning to streamline processes and improve efficiency. The future may hold more transformative changes, but for now, the focus is on leveraging digital tools to enhance the traditional construction methods that have persisted for decades.